Participants in the inspection included: Mr. Nguyen Van Yen, Head of Legal - Inspection Department, Department of Labor Safety, Ministry of Labor, War Invalids and Social Affairs; Mr. Pham Hoang Minh, Deputy Head of Legal - Inspection Department, Department of Labor Safety, Ministry of Labor, War Invalids and Social Affairs; Ms. Chuc Thu Trang - Specialist of Labor Protection Policy Department, Department of Occupational Safety, Ministry of Labor, War Invalids and Social Affairs, Ms. Le Thi Xiem, Specialist of Legal Department - Inspector of Department of Labor Safety, Ministry of Labor - Invalids and Society; on the side of Sigma Engineering: Mr. Yatsu Takabumi - Chairman of the Company, Mr. Ha Dung - Deputy Director of the Company, Mr. Nguyen Van Hiep, Head of the Safety Department, and representatives of other departments attended the inspection.
Main contents include:
1. Employee policies:
- Inspect the implementation of regimes: Inspect the implementation of social insurance, health insurance, unemployment insurance and other employee benefits.
- Work and rest regime: Check compliance with regulations on working time, rest time, annual leave, and allowances.
- Welfare policy: Evaluate welfare policies such as mid-shift meals, protective clothing, housing, or transportation support for workers.
2. OSH plan:
- Develop and implement plans: Evaluate the development of the annual OSH plan, including specific objectives and implementation measures.
- Assignment of responsibilities: Check the assignment of specific responsibilities to departments and individuals in implementing the OSH plan.
- Resources and budget: Evaluate the allocation of resources and budget for OSH activities.
3. Control OSH risks:
- Risk assessment: Review the process of assessing and analyzing risks in the workplace, including identifying hazards and assessing risk levels.
- Control measures: Check the risk control measures that have been implemented, such as replacement, technical controls, administrative controls, and personal protective equipment.
- Monitor and update: Evaluate the monitoring system and update risk control measures, ensuring they are always consistent with the actual situation.
4. Respond to emergency situations:
- Response plan: Check the emergency response plan, including incident scenarios and corresponding handling measures.
- Training and drills: Evaluate the organization of periodic training sessions and drills to improve workers' emergency response skills.
- Emergency equipment: Check the readiness and maintenance of emergency response equipment such as fire extinguishers, fire alarm systems, and rescue equipment.
5. Work safety training:
- Training program: Evaluate the content and quality of occupational safety training programs, ensuring they are suitable for each employee and the nature of the job.
- Training frequency: Check the frequency of organizing training courses, including basic training, periodic training, and advanced training.
- Training effectiveness: Evaluate the effectiveness of training through testing the knowledge and skills of workers after participating in courses.
6. Processes and measures to ensure safety:
- Process development: Evaluate the development of processes and measures to ensure safety in the workplace, including safe working procedures, equipment maintenance procedures, and troubleshooting procedures.
- Implementation and compliance: Check the implementation and compliance with proposed processes and measures, ensuring they are applied correctly and effectively.
- Continuous improvement: Evaluate the process of continuously improving safety processes and measures based on feedback from workers and previous inspections.
7. Equip personal protective equipment for workers:
- Periodically provide PPE for workers such as shoes, hats, and protective clothing. In addition, depending on the specifics of the job, additional equipment will be provided: gloves, masks, goggles, face shields, gas mask….
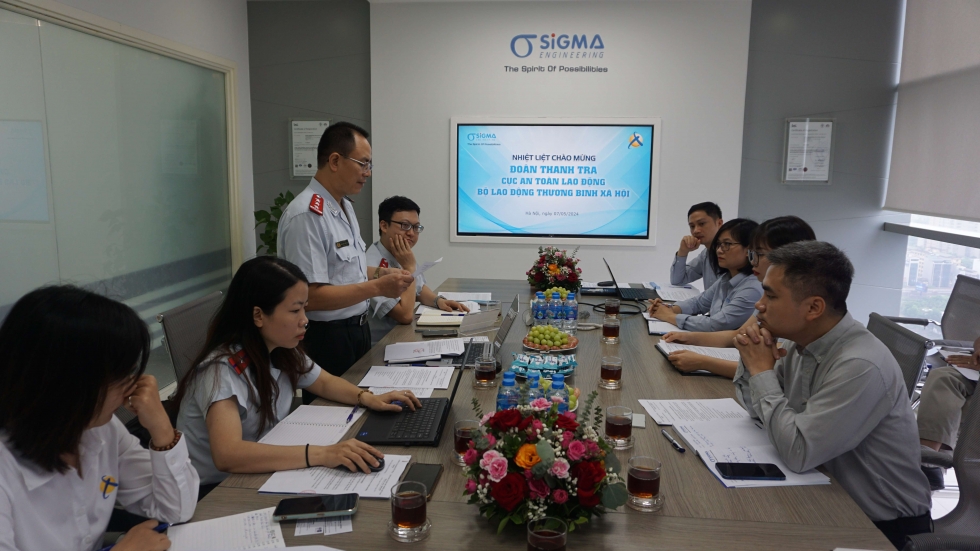
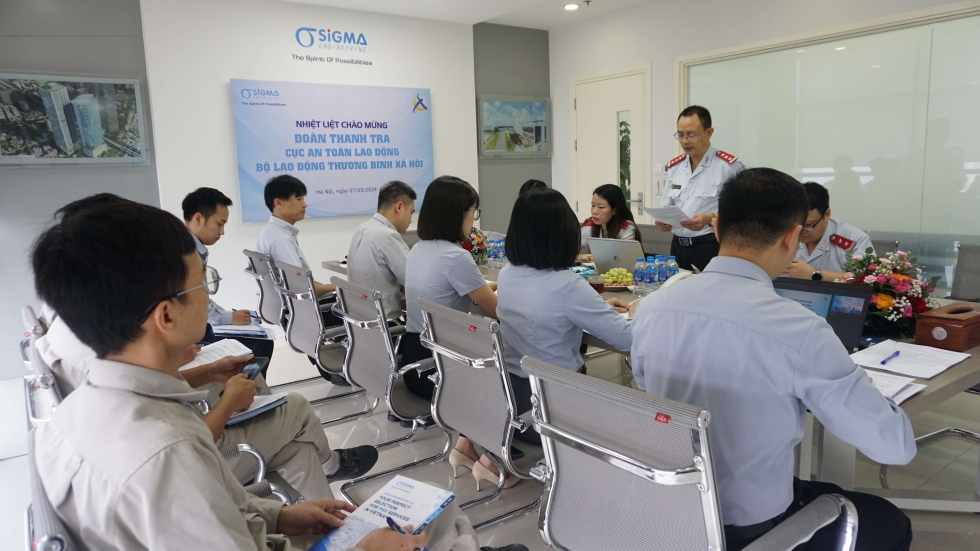
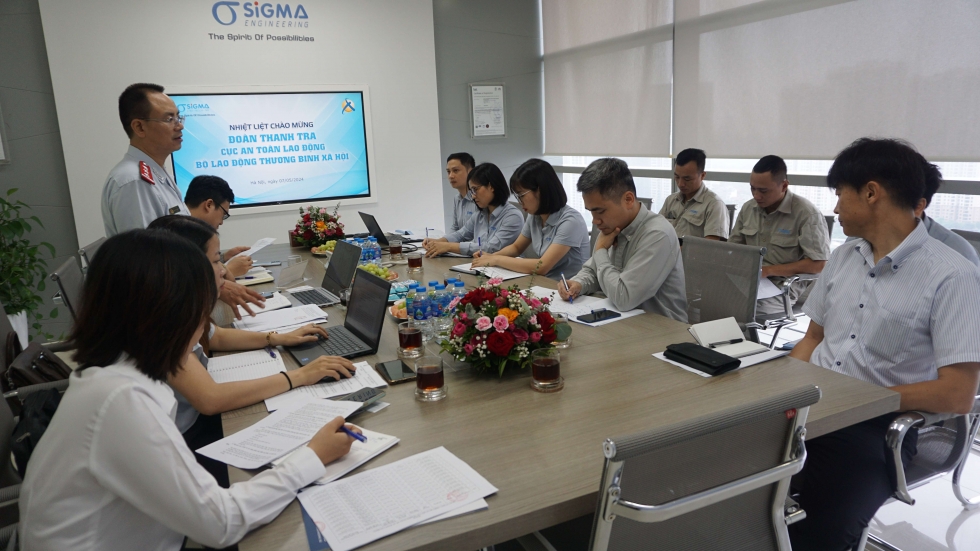
Some pictures during the inspection
Through inspection work of the Department of Safety - Ministry of Labor, War Invalids and Social Affairs, Sigma has complied with regulations on labor safety, health protection and ensuring safe working conditions for all employees, contributing to building a safe and healthy working environment.