The key to the successful operation of a cable system is to select the most suitable cable for the application, make a correct installation, and perform the required maintenance.
In this technical article, discussion is based on the correct cable selection and application for power distribution and utilization.
Cable selection can be based upon the following five key factors:
- Cable installation
- Cable construction
- Cable operation (voltage and current)
- Cable size
- Shielding requirements
1. Cable installation
Cables can be used for outdoor or indoor installations depending upon the distribution system and the load served.
A good understanding of local conditions, installation crews, and maintenance personnel is essential to assure that the selected cable system will operate satisfactorily! Many times cable insulation is damaged or weakened during installation by applying the incorrect pulling tensions.
Designs of conduit systems not only should minimize the number of conduit bends and distances between manholes but also should specify the pulling tensions.
The inspection personnel should ensure that installation crews do not exceed these values during installations. It is also important that correct bending radius be maintained in order to avoid unnecessary stress points. Once a correct installation is made, routine inspection, testing, and maintenance should be carried out on a regular basis to chart the gradual deterioration and upkeep of the cable system.
Cable systems are the arteries of the electric power distribution system and carry the energy required for the successful operation of a plant. Following is a brief discussion on cable installation and maintenance.
There are several types of cable systems available for carrying electrical energy in a given distribution system. The selection of a particular system may be influenced by local conditions, existing company policies, or past experience.
No set standards or established guidelines can be given for the selection of a particular system.
2. Cable construction
Selection and application of cable involves the type of cable construction needed for a particular installation. Cable construction involves conductors, cable arrangement, and insulation and finish covering.
2.1 Conductors
Conductor materials such as copper and aluminum should be given consideration with regard to workmanship, environmental conditions, and maintenance. The requirements for aluminum conductors with regard to these factors are more critical than for copper conductors.
Cable conductors should be selected based upon the class of stranding required for a particular installation.
2.2 Cable arrangement
Conductors can be arranged to form single-conductor or three-conductor cable. There are certain advantages and disadvantages to both types of arrangements. Single conductors are easier to install, easier to splice, and allow the formation of multiple-cable circuits.
On the other hand, they have higher reactance than three-conductor cable. Shielded single conductors carry high shield currents, and consideration must be given to preventing overheating of the cable.
Single-conductor cables are subject to considerable movement owing to the mechanical stresses produced by the short circuit currents or high inrush currents. Three-conductor cable with an overall jacket has the lowest reactance, and voltage stress distribution is balanced owing to equivalent spacing between conductors.
The availability of ground wire in three-conductor cable or a separate ground wire with single-conductor cable is an important consideration. Since the ground conductor in three-conductor cable construction provides the lowest impedance path, it offers a good system ground.
Similarly, a separate ground in the same conduit as the power conductors provides a better ground return path than a ground path via the equipment or building steel.
The selection and application of a cable system should be based on correct selection of the type of cable arrangement required for the purpose.
2.3 Insulation and finish covering
The selection of cable insulation and finish covering is normally based on the type of installation, ambient operating temperature, service conditions, type of load served, and other criteria as applicable. In many installations unusual conditions may be prevalent, such as corrosive atmosphere, high ambient temperature, insect and rodent hazard, presence of oil and solvents, presence of ozone, and extreme cold.
In certain applications, two or more of these unusual conditions may be present, in which case the selection of suitable cables becomes much more difficult.
3. Cable operation
The insulation of the cable must be able to withstand the voltage stresses experienced during normal and abnormal operating conditions. Therefore the selection of the cable insulation should be made on the basis of the applicable phase-to-phase voltage and the general system category which are classified as either 100%, 133%, or 173% insulation levels.
These insulation levels are discussed as follows:
100% level:
Cables in this category may be applied where the system is provided with relay protection which normally clears ground faults within 1 minute. This category is usually referred to as the grounded systems.
133% level:
Cables in this category may be applied where the system is provided with relay protection which normally clears ground faults within 1 hour. This category is usually referred to as the low resistance grounded, or ungrounded systems.
173% level:
Cables in this category may be applied where the time needed to de-energize the ground fault is indefinite. This level is recommended for ungrounded and for resonant grounded systems.
The current capacity that the cable needs to carry is determined by the load it serves.
The NEC is very specific in terms of sizing conductors for systems operating below 600 V. The current carrying ability of cable is based upon an operating ambient temperature. When cables are installed in multiple duct banks, it is essential to derate the cable current capacity in order not to exceed its thermal rating.
In cases where cables may be load cycled, the current carrying capacity may be calculated by the following formula:
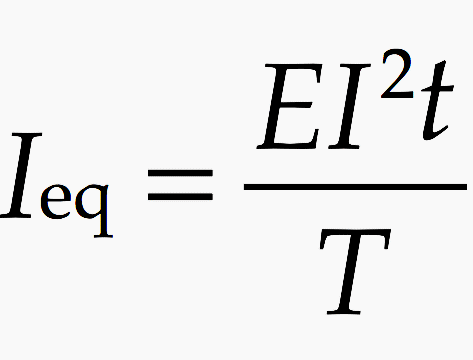
where:
- Ieq is the equivalent current carrying capacity
- I is the constant current for a particular time period
- t is the time period of constant current
- T is the total time of duty cycle
- E is the voltage of the cable
The equivalent current carrying capacity should be used for selecting the conductor size for thermal withstand.
4. Cable size
The selection of cable size is based upon the following factors:
- Current carrying capacity
- Voltage regulation
- Short circuit rating
These factors should be evaluated before selecting a cable size! In many instances, voltage regulation and short circuit rating factors are overlooked. This oversight can result in danger to property and personnel, as well as destruction of the cable itself.
4.1 Current carrying capacity
The current carrying capacity of a cable is based upon its thermal heating. The NEC publishes tables listing the current capacity for various-sized cables. The ICEA publishes current ratings for various types of insulations and installation conditions.
If it is required to carry capacity larger than 500 MCM, it is normal practice to parallel two smaller conductors.
The current rating of cable is based upon certain spacing to permit thermal dissipation. If this spacing is smaller where the cable is to be installed, then derating of cable is required.
4.2 Voltage regulation
In correctly designed electrical power systems, voltage regulation is usually not a problem. Voltage drops for excessively long runs at low voltage should be checked to ensure correct load voltage. In rotating loads, checks should be made both on steady-state voltage regulation and during starting.
The NEC specifies a 5% limit of voltage drop for electrical power distribution systems.
4.3 Short circuit rating
The cable size selected should be checked for short circuit withstand capability, which should be based upon the circuit opening time for short circuit condition. In other words, the cable should hold without any thermal damage to it until such time as the fault can be removed by the switching device, such as a circuit breaker or fuse.
5. Shielding
In selecting and applying cables at medium voltage, a major consideration involves whether the cable should be shielded or non-shielded. The conditions under which shielded cable is to be selected and applied is explained in the following discussion.
The application of shielded cable involves the following considerations:
- Type of insulation system
- Whether the system neutral is grounded or ungrounded
- Safety and reliability requirements of the system
In power systems where there is no shield or metallic covering, the electric field is partly in the air and partly in the insulation system! If the electric field is intense, such as in the case of high and medium voltage, surface discharges will take place and cause ionization of the air particles. The ionization of air causes ozone generation, which can deteriorate certain insulations and finish coverings.
In the application of non-shielded cable on ungrounded systems, damage to insulation or jackets can be caused by leakage current if the surface of the cable is moist or covered with soot, grease, dirt, or other conducting film.
In cases where portable cables, cable assemblies, or exposed overhead cable installations are used and may be handled by personnel, serious safety hazards may exist if non-shielded cable is used!!
There are five fundamental constituents that make a cable: conductor, insulation, shield, filler and strength member
Shielding should be considered for nonmetallic cable operating in excess of 2kV where any of the following conditions exist:
- Damp conduits
- Connection to aerial wires
- Transition from a conducting to a nonconducting environment (such as from moist to dry earth)
- Dry soil
- Dirty environment containing soot, salt, and other contaminants
- Where safety to personnel is required
- Where radio interference is expected
The ICEA has set up voltage limits above which insulation shielding is required for rubber and thermoplastic-insulated cables. These values are shown in Table 1.
The insulation shield must be grounded at least at one end and preferably at two or more points. The cable shield must be grounded also at all terminations, splices, and taps with stress cones. The shield should be operated at ground potential.
Multiple grounding will ensure safety and reliability of the cable circuits. The ground path from the shield should be of low resistance to keep the shield near ground potential.
TABLE 1: Insulation Shielding Requirements for Rubber and Thermoplastic-Insulated Cables
Reference: Electrical Power Equipment Maintenance and Testing by Paul Gill (Purchase hardcopy from Amazon)